A fundamental part of the supply chain is planning the freight movement around your purchase or sale. Since the global pandemic, Australia has been facing an import/export crisis, as Covid-19 has destabilised the global freight supply chain, delayed shipments and caused a rapid rise in freight costs. Additionally, a surge in demand for containerised cargo and extreme congestion across the global supply chain has caused significant delays and disruption, placing immense pressure on Australian importers and exporters.
Since the on-going effects of Covid, it is essential for you to assess how changing timelines could impact your purchase or sale. If you’re looking for information on the changes and effects in the freight industry due to Covid-19 and seeking guidance on re-planning your freight shipment, you’re in the right place. Below, Gava Australia will outline why freight timelines have changed since the pandemic and provide tips on re-planning and factoring in the changing timelines to your purchase or sale.
Why do Freight Timelines Change?
Prior to the global pandemic, delays in freight timelines still occurred. However, this was mainly around the peak seasons, as there is greater demand. The peak seasons occur in January-February due to the Chinese New Year, June-September, due to the European summer, and November-January due to Christmas and New Year.
When creating a booking to ship your cargo, it is not always guaranteed to make that exact vessel. These vessel changes are out of any freight forwarder’s control and can be extremely frustrating for both the client and the freight forwarder! Below, we have outlined several factors explaining why transit times via Sea Freight may alter from when you book to when you receive your cargo (pre Covid).
Why did my Cargo Miss the Vessel?
- Missing Cut off Times – This is a fixed date when the cargo must be booked in at the port. If the shipment misses the cut-off time for the intended vessel, it cannot be shipped. This is one of the most significant factors that will affect your timeline. If you miss the cut-off, you will be waiting up to two weeks before the next vessel.
- Blank Sailing – This occurs when a vessel is cancelled. This can be when one leg of the journey is cancelled or the entire voyage. Blank sailing is entirely at the shipping line’s discretion, and we, the freight forwarders, are notified last minute without warning, despite the bookings in place.
- Lack of Equipment – If your goods require specialised equipment for transport, you could experience some delays. For instance, if the shipping line at your export port does not have the required equipment, including flat-racks, open tops, reefers, or even standard GP Containers.
- Container Rolls – Rolled cargo is when the goods have not been loaded onto its intended vessel. The main reason for this is that the vessel ran out of capacity. Vessels often run out of capacity due to carriers overbooking spots on vessels.
- Delays at Transhipment Ports – If you choose to ship your cargo via a transhipment route, your shipment could face extended delays. Transhipping refers to shipping your goods to an intermediate location before its final destination. Unfortunately, delays can occur at busy transhipment ports (Singapore & Malaysia), especially during peak shipping season.
- Delays at Customs – Extended delays can significantly impact your shipping timeline. Two key factors that contribute to a delay at customs include:
- 1. Having to inspect your Cargo – This may be because the cargo has caused some concern to the Australian Quarantine Inspection Service (AQIS), and the goods could be at risk of stink bugs or need to be fumigated; and
- 2. Lacking required documentation and paperwork – Including Commercial Invoice or Packing Declaration. Having the correct paperwork when organising a shipment is essential to avoid unnecessary delays.
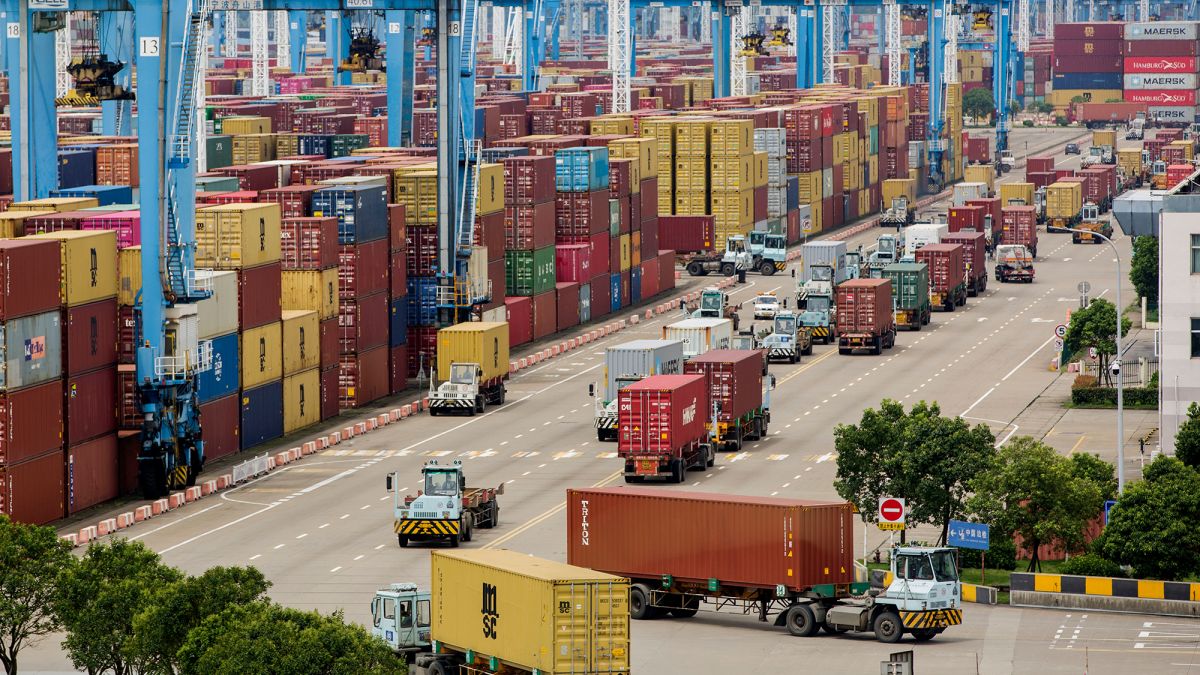
Drastic Timeline Changes since Covid-19:
The Coronavirus disease (COVID-19) may be declining; however, the aftermath of the pandemic has severely disrupted the economic supply chain and continues to affect the freight forwarding industry. During the past few years, delays in the container shipping industry have had a flow-on effect on many sectors around the world.
As mentioned above, your cargo is not guaranteed to make the same vessel it is booked on due to numerous factors. Since Covid and its contribution to the supply chain delays, the chances of your cargo making it onto its allocated vessel have diminished even more.
What Were Shipping Times Like Before Covid?
- Vessels were regularly departing every week.
- The repositioning of empty containers around the world were moving as normal.
- Manufacturing goods in factories were as usual.
- Suppliers received the materials in a timely manner to commence the production of their goods.
- Port operations were smooth and efficient. There was minor port congestion, and delays were only expected in certain countries in particular seasons.
- Container shipping rates and overall freight rates were consistent.
Effect of Covid-19 on The Shipping Industry:
Since COVID, vessels are experiencing delays due to the freight industry’s severely impacted supply chain system. With international border closures and increased consumer demand for imports, Australian imported products have been affected exponentially. A further breakdown of the domino effect of the supply chain includes:
How Shipping Delays have had a Direct Impact on The Freight Supply Chain System:
- Worldwide Factory Closures: The factory closures (due to COVID) have delayed manufacturing goods for export/import. Therefore, suppliers are late receiving primary goods to produce the products.
- Delayed Shipping Times: The shipping time on orders has been significantly delayed, as Covid has affected the number of international shipping container arrivals.
- Port Congestion: The high docking fees and port congestion have caused significant delays, with some ships waiting over a week outside the port (at sea) before they can berth and unload.
- Limited Container Capacity and Empty Container Parks: The rotation for returning empty containers back to Origin (Asia, Europe, America) from Australia has significantly diminished since Covid. It is very difficult to find empty containers, as they are often stuck on vessels, at the ports, or in warehouses with cargo from the previous shipment waiting to be unloaded.
- Changed Sailing Schedules: Instead of vessels departing weekly, they are now leaving fortnightly. Therefore, only 2 ships are sailing per month.
- Vessel Capacity: If your cargo misses its scheduled vessel (due to any reason), the next vessel (departing in 2 weeks) is usually fully booked and may experience problems trying to make that vessel.
- Cancelled and Bypassed Shipping schedules: COVID delays have caused cancelled or bypassed shipping schedules, which has significantly impacted delivery times to consumers.
- Additional Delays: Australia has seen further delays in quarantine, fumigation, and customs clearance.
- Self-Isolation: Australia has experience delays at the ports and airports, as workers have been made to self-isolate (14 days) due to contracting Covid. With less staff working at the docks, it takes longer to load and unload the containers.
- Staff Strikes: The strikes have caused delays in the freight supply chain, as there are fewer workers at the port and airports to keep the supply chain moving.

As you can see, the delays go through the supply chain from manufacturing, shipping, and exporting to the trucks waiting hours to collect containers. Another example of delayed scheduling was seen during the port congestion in Shanghai, China. Over 400 vessels were stuck at the wharf in Shanghai. Due to this congestion, the vessel could not be unloaded, making the cargo on the ship late to the clients. Additionally, the ship and the empty containers on these vessels were also stuck on the water, missing their scheduled date, and making them late to their next destination. So even though the congestion is occurring in China, Europe, and America, it’s still impacting the timeline on shipments arriving in Australia.
Unpredicted Events causing extreme delays within the Freight Industry:
Unfortunately, there are extreme cases where unpredictable events occur and cause significant delays within the Freight industry. It is impossible to plan for these events, as they usually happen unexpectedly; however, it is always a good idea to have Marine Insurance in case your goods are lost or damaged. Below are several examples of unpredicted events that have drastically affected the freight transit timeline.
- Global Financial Crisis
- Natural Disasters & Severe weather – e.g., Brisbane Floods
- Economic Trade War: US-China
- Covid-19
- Russia and Ukraine War
Tips on Factoring in Freight Timeline Changes:
- Allow at least an additional week or two for Sea Freight.
That way, you will be guaranteed a buffer of two weeks to allow for any unexpected contingencies that may occur throughout your shipment.
- Caveat your Purchase and Sale
To avoid any legal issues associated with your cargo being delayed, caveat your purchase or sale as ‘Subject to delays’ or ‘Subject to the goods being available’. This way, you are covered in case of any unexpected delays. It is always recommended to consult a legal professional when negotiating or drafting a sales contract. Do not rely on delivery times as the container shipping situation is likely to have impact on your supply chain.
- Air Freight is a more Reliable, Timely Solution to Shipping for Urgency
If your cargo is required urgently, you should usually select Air Freight as your method of shipment and use a direct route to avoid transhipment delays. However, Air Freight is more expensive, so this must also be considered.
- Consult a Freight Forwarder to ensure you are not held up by Customs and other unknown Delays when partaking in International Shipping
When partaking in International Shipping, it is essential to understand all factors that may contribute to delays when receiving your cargo. For instance, in Customs, it is important to have the correct documentation and paperwork prepared to prevent delays. This includes Commercial Invoice and Packing Declaration forms. Having these documents ready will help avoid any unnecessary delays. Other delays may include fumigation, missed timeslots, demurrage, detention, and wharf storage.
As explained above, the Covid-19 outbreak has significantly impacted the freight forwarding industry and placed immense pressure on Australian importers and exporters. Gava Australia wants to inform our customers that their initial plan of placing their order, waiting for the factory to produce their goods, and waiting for the freight time, must be re-planned, reengineered and changed, as we are currently experiencing extreme delays in the industry. Whilst it is impossible to predict the duration of the current predicament, and when things return to “normal”, expectations for shipping are uncertain. However, we constantly monitor the situation and work closely with our global agents and suppliers to achieve the best solutions to minimise the impact on our client’s supply chain.
At Gava Australia, we will do our absolute best to deliver your goods on time and keep you well informed of any changes or issues that arise in the industry. We understand these delays are frustrating and upsetting; however, please understand that missed vessels and delayed cargo are out of any freight forwarder’s control, and unfortunately, we must be the bearers of bad news. So, we ask that you please take this into consideration!
Still need information? You’ve come to the right place. Book a Free Consultation with our Gava Australia Team.
Should you have any questions, please don’t hesitate to contact us. For additional updates and information on the Latest News in the industry, please visit our new Gava Website https://www.gava.com.au/blog/